Hình 1. Sơ đồ biến dạng dẻo lớp bề mặt
Khi lăn ép dụng cụ lăn ép là con lăn sẽ ép vào bề mặt chi tiết cần gia công và di chuyển dọc phôi với bước tiến là S, phôi quay với số vong quay là n
p (hình 1.a). Sơ đồ quá trình lăn ép ngang bằng tấm phẳng được thể hiện trên hình 1b. Tấm dưới đứng yên, tấm trên di chuyển xuống giá trị nén (t), sau đó tấm trên di chuyển sang phải cho đến khi phôi di chuyển một vòng, tức là quá trình lăn ép xảy ra trên toàn bộ bề mặt trụ của chi tiết. Sơ đồ miết ép dao động được thể hiện trên hình 1.c, khi miết ép phôi sẽ quay tròn, dụng cụ miết ép sẽ ép vào bề mặt của phôi, dụng cụ miết ép chuyển động dọc phôi với bước tiến S đồng thời chuyển động tịnh tiến lên xuống.
Để so sánh chất lượng lớp bề mặt của các chi tiết đã được hóa bền, nghiên cứu được thực hiện trên các mẫu hình trụ có đường kính 20 mm, vật liệu C35. Việc lăn ép bằng con lăn được thực hiện trên máy tiện 1K62 với con lăn hình trụ làm bằng thép gió P9, đường kính 40 mm với bán kính biên dạng r = 4 mm. Lăn ép ngang bằng tấm phẳng được thực hiện trên máy cán phẳng [7]. Miết ép dao động được thực hiện trên máy tiện 1K62, bán kính biên dạng của dụng cụ miết ép r = 4 mm; vật liệu – thép gió P9.
Khi hóa bền bằng các phương pháp BDD khác nhau, các thông số và chế độ lăn ép được chọn như sau: Lăn ép bằng con lăn trên máy tiện: Bước tiến dọc S = 0,14 mm/vòng, chiều sâu lăn ép t = 0,12 mm, số vòng quay phôi n
p = 120 vòng / phút. Lăn ép ngang bằng tấm phẳng: Phôi được thực hiện 3 vòng với tốc độ tấm chuyển động 7,5 m/phút, chiều sâu lăn ép t = 0,12 mm. Chế độ miết ép dao động: Số vòng quay phôi n
p = 120 vòng / phút; tần số dao động của dụng cụ miết ép n
lx = 40 HTK/phút; chiều sâu miết ép t = 0,12 mm; biên độ dao động của dụng cụ e = 30 mm; bước tiến của dụng cụ miết s = 0,12 mm/vòng; góc quay dụng cụ α = 45
0.
2.2. Kết quả và thảo luận
2.2.1. Đánh giá độ nhám
Độ nhám bề mặt được xác định trên máy đo độ nhám FormTalySurfi200, máy này dùng để đo độ nhám và sai lệch về hình dáng hình học của chi tiết máy. Trên mỗi đoạn của chi tiết đo ở 3 vị trí cách nhau 120
o, chiều dài đo khoảng 10mm rồi lấy giá trị độ nhám Ra trung bình.
Hình 2 thể hiện giá trị độ nhám Ra tùy thuộc vào phương pháp hóa bền.
Kết quả đo độ nhám cho thấy độ nhám tốt nhất đạt được bằng phương pháp lăn ép ngang với các tấm phẳng, sau đó là miết ép dao động. Độ nhám bề mặt của chi tiết sau khi cán ngang bằng tấm phẳng nhỏ hơn 7 - 9 lần so với độ nhám của bề mặt của chi tiết hóa bền bằng các phương pháp khác. Độ nhám bề mặt của chi tiết sau khi cán ngang bằng tấm phẳng nhỏ hơn độ nhám khi hóa bền bằng các phương pháp khác có liên quan đến hai lý do, một là điều kiện thuận lợi cho sự tiếp xúc của dụng cụ với bề mặt được hóa bền, hai là tác động lặp đi lặp lại của các tấm trên lớp bề mặt của chi tiết. Kết quả trên hoàn toàn phù hợp với các kết quả được công bố trong [3].
Hình 2. Sự phụ thuộc độ nhám vào phương pháp hóa bền
I. Độ nhám trước khi hóa bền; II. Lăn ép bằng con lăn; III. Lăn ép ngang; IV. Miết ép dao động
2.2.2. Tổ chức tế vi và kích thước hạt
Để nghiên cứu tổ chức tế vi của kim loại cần tiến hành phân tích kim tương, rồi sử dụng kính hiển vi MICROMED MET 2 kết hợp với máy tính sử dụng chương trình Toup View để quan sát trực tiếp và chụp ảnh tổ chức tế vi của kim loại trên màn hình máy tính - với mức phóng to từ 100 đến 1000 lần.
Hình 3 cho thấy các hình ảnh về cấu trúc vi mô của các chi tiết sau khi hóa bền bằng các phương pháp khác nhau.
Cả ba phương pháp hóa bền bằng biến dạng dẻo đều ảnh hưởng đến sự thay đổi cấu trúc vi mô ở lớp bề mặt. Sau khi hóa bền, các hạt được kéo ra theo hướng biến dạng chính và được nghiền nát. Trong lớp bề mặt kim loại bị biến dạng dẻo, các hạt tạo thành mới có kích thước nhỏ hơn và có một hướng nhất định. Các hạt bị kéo dài theo hướng biến dạng chính, điều này có thể được đánh giá qua hình ảnh cấu trúc hạt khi phóng to. Do chuyển động dọc của dụng cụ so với phôi trong quá trình lăn con lăn và làm mịn dao động, các hạt được kéo ra theo hướng dọc mạnh hơn so với hướng ngang. Chuyển động dọc của dụng cụ so với trục của phôi tạo thành một làn sóng kim loại ép đùn, cản trở chuyển động tương đối của vật liệu giữa dụng cụ và phôi theo hướng dọc; một lực dọc đáng kể phát sinh, đã gây ra biến dạng của các hạt dọc theo trục của phôi.
Hình 3. Cấu trúc vi mô của các chi tiết sau khi hóa bền bằng các phương pháp khác nhau
Sự thay đổi kích thước hạt chỉ xảy ra ở phía ngoài lớp bề mặt, vùng trung tâm thực tế không bị biến dạng dẻo và hạt không thay đổi kích thước. Chiều sâu lớp biến dạng tính từ phía ngoài lớp bề mặt khoảng 0,15 - 0,2 mm khi miết ép và cán ngang với các tấm phẳng còn khi lăn ép bằng con lăn là 0,11 mm. Kết quả trên phù hợp với các kết quả được công bố trong [3].
2.2.3. Độ cứng tế vi và chiều sâu lớp biến cứng
Độ cứng tế vi đo theo phương hướng kính mặt cắt ngang của mẫu, sử dụng máy đo độ cứng tế vi PMT-3, đo 14 điểm trên một đường thẳng từ ngoài vào tâm.
Hình 4 cho thấy chiều sâu lớp biến cứng sau khi hóa bền bằng các phương pháp khác nhau.
Hình 4. Chiều sâu lớp biến cứng sau khi hóa bền bằng các phương pháp khác nhau
1. Trước khi hóa bền; 2. Lăn ép bằng con lăn; 3. Lăn ép ngang; 4. Miết ép dao động
Độ cứng tế vi của lớp bề mặt sau khi hóa bền bằng các phương pháp biến dạng dẻo tăng khoảng 18 - 25%. Trong các phương pháp hóa bền trên, độ cứng tế vi lớn nhất đạt được bằng phương pháp lăn ép ngang bằng tấm phẳng (2782 MPa), vì phương pháp này có biến dạng dẻo lớn, còn phương pháp lăn ép bằng con lăn độ cứng tế vi tăng là nhỏ nhất 2627 MPa. Chiều sâu lớp biến cứng từ 0,6 – 0,8 mm tính từ phía ngoài của lớp bề mặt.
2.2.4. Độ cứng lớp bề mặt
Để xác định độ cứng Rockwell sử dụng máy đo độ cứng HBRV-187.5, trên mỗi đoạn mẫu đo 6 điểm nằm trên hai vòng tròn, độ cứng của mỗi đoạn được lấy là giá trị độ cứng được lấy là giá trị trung bình của sáu điểm được đo.
Hình 5 cho thấy sự thay đổi độ cứng bề mặt tùy thuộc vào phương pháp hóa bền.
Hình 5. Sự phụ thuộc độ cứng vào phương pháp hóa bền
I. Độ cứng trước khi hóa bền; II. Lăn ép bằng con lăn; III. Lăn ép ngang; IV. Miết ép dao động
Độ cứng tốt nhất đạt được bằng phương pháp lăn ép ngang bằng các tấm phẳng và độ cứng thấp nhất đạt được bằng phương pháp lăn ép bằng con lăn. Đồng thời, độ cứng tăng lần lượt là 11,3 % và 5,3 %. Điều này được giải thích là do trong quá trình lăn ép ngang bằng các tấm phẳng lớp bề mặt bị biến dạng nhiều lần và ở mức độ lớn hơn so với khi lăn ép bằng con lăn. Với quá trình miết ép dao động, độ cứng tăng 7,9 % so với độ cứng ban đầu.
2.2.4. Ứng suất dư
Kết quả đo ứng suất dư bằng phương pháp tia X được trình bày ở bảng 2.
Bảng 2 - Ứng suất dư trên lớp bề mặt của chi tiết với các phương pháp hóa bền khác nhau
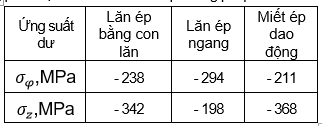
Cả ba phương pháp hóa bền bằng biến dạng dẻo trên đều hình thành ứng suất dư nén trên lớp bề mặt của chi tiết. Ứng suất dư dọc trục lớn nhất đạt được khi miết ép dao động, rồi đến lăn ép bằng con lăn và cuối cùng là lăn ép ngang, tuy nhiên ứng suất tiếp tuyến lớn nhất được hình thành trong quá trình lăn ép ngang bằng tấm phẳng, còn nhỏ nhất là miết ép dao động. Kết quả trên hoàn toàn phù hợp với các kết quả được công bố trong [3].
3. KẾT LUẬN
- Kết quả nghiên cứu cho thấy độ nhám thu được bằng phương pháp miết ép dao động nhỏ hơn so với khi lăn ép bằng con lăn, nhưng lớn hơn khi lăn ngang bằng các tấm phẳng.
- Sự thay đổi kích thước hạt chỉ xảy ra ở lớp bề mặt, còn vùng trung tâm thực tế không bị biến dạng dẻo và hạt không thay đổi kích thước. Diện tích hạt biến dạng đáng kể kéo dài đến độ sâu 0,15 - 0,25 mm khi lăn ép ngang bằng các tấm phẳng và miết ép dao động, còn khi lăn ép bằng con lăn 0,1 mm.
- Độ cứng vi mô và độ cứng thu được khi miết ép dao động lớn hơn so với lăn ép bằng con lăn, nhưng nhỏ hơn so với lăn ép ngang các tấm phẳng.
- Chất lượng bề mặt sau khi miết ép dao động tốt hơn khi lăn ép bằng con lăn nhưng lại kém hơn khi lăn ép ngang bằng tấm phẳng.
TàI LIỆU THAM KHẢO
[1]. Zaides S.A, Emelyanov V.N, Popov M.E; Kropotkina E.U, Bubnov A.S (2013), Gia công biến dạng chi tiết dạng trục, Nhà xuất bản Đại học IrGTU, 449 trang.
[2]. Pashev D. D. (1987). Hóa bền bằng biến dạng dẻo. Nhà xuất bản kỹ thuật Matxcova, 152 trang.
[3]. Poliak M. S. (1995). Công nghệ hóa bền. Nhà xuất bản kỹ thuật Matxcova, 688 trang.
[4]. Baltep M. A. (1987). Hóa bền chi tiết máy. Nhà xuất bản kỹ thuật Matxcova, 184 trang.
[5]. Smeliaski V. M. (2002). Hóa bền cơ học lớp bề mặt của chi tiết máy bằng phương pháp biến dạng dẻo. Nhà xuất bản kỹ thuật Matxcova, 299 trang.
[6]. Zaides S.A, Nguyen Van Hinh (2017) Ảnh hưởng của các thông số công nghệ đến độ nhám bề mặt của chi tiết máy sau khi miết ép dao động. Tạp chí khoa học IrGTY, số 4 trang 22-29.
[7]. Zaides S.A., Ngô Cao Cường, Lê Hồng Quang (2018). Đánh giá chất lượng lớp bề mặt khi hóa bền bằng biến dạng dẻo với các con lăn có thiết kế khác nhau. Tạp chí khoa học IrGTY, số 1 trang 30-38.
[8]. Zaides S.A., Phạm Đắc Phượng (2016). Đánh giá chất lượng của chi tiết máy hình trụ sau khi lăn ép ngang bằng tấm phẳng. Tạp chí khoa học Công nghệ hóa bền và phun phủ, số 7 trang 14–18.