Việc nghiên cứu hiệu ứng bão hòa của động cơ và sự tương tác giữa điện tử công suất với hệ thống điều khiển đóng vai trò quan trọng trong việc phát triển bộ điều khiển hiệu quả. Để đạt được điều này, đã kết hợp phân tích phần tử hữu hạn 3D, động lực học đa vật thể, và hệ thống điều khiển, giúp dự đoán và tránh được các hiệu ứng phục hồi lỗi theo dõi, kéo, định vị và tích lũy.
Phân tích phần tử hữu hạn 3D giúp mô phỏng chi tiết cấu trúc và hành vi động lực của các thành phần trong hệ thống. Động lực học đa vật thể cung cấp cái nhìn sâu hơn về tương tác giữa các thành phần cơ khí và động cơ, trong khi hệ thống điều khiển đảm bảo rằng các yếu tố này hoạt động hài hòa với nhau. Sự kết hợp này không chỉ dự đoán chính xác các lỗi có thể xảy ra mà còn giúp điều chỉnh kịp thời để tránh các vấn đề tiềm ẩn.
Nhờ các phương pháp tiên tiến này, máy phay CNC có thể hoạt động với hiệu suất cao hơn và độ ổn định tốt hơn trong quá trình gia công, đảm bảo chất lượng sản phẩm cuối cùng và tối ưu hóa quy trình sản xuất.
a. Cải thiện tốc độ & độ chính xác: Tối ưu hóa sự tương tác động của các thành phần hệ thống bằng cách kết hợp các yếu tố bao gồm:
- Phân tích phần tử hữu hạn 3D
- Động lực học đa vật thể
- Mô phỏng hệ thống
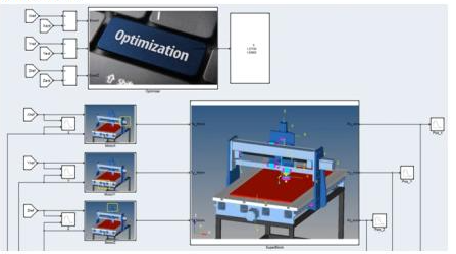
Hình 1. Kết hợp mô phỏng cơ điện tử và cơ khí
b. Tối ưu hóa kết cấu cơ khí, hệ thống cơ điện tử
- Kết cấu:
+ Lựa chọn kết cấu tối ưu trên máy: Đòi hỏi phân tích kỹ lưỡng về khả năng chịu tải và độ bền của vật liệu để đảm bảo độ ổn định và tuổi thọ của hệ thống.
+ Tải trọng tác động: Xem xét các lực tác động lên kết cấu, bao gồm cả tải trọng tĩnh và động, để đảm bảo hệ thống hoạt động ổn định dưới các điều kiện khác nhau.
+ Biến dạng ngoài thông số kỹ thuật: Đánh giá và kiểm soát các biến dạng không mong muốn có thể ảnh hưởng đến độ chính xác và hiệu suất của hệ thống.
- Truyền động:
+ Độ chính xác: Cần thiết lập các phương pháp đo lường và điều chỉnh để đảm bảo các bộ phận truyền động hoạt động với độ chính xác cao nhất.
+ Dao động: Giảm thiểu các dao động không mong muốn thông qua việc cân bằng và tối ưu hóa các bộ phận cơ khí.
+ Tiếng ồn: Kiểm soát và giảm thiểu tiếng ồn phát sinh từ các bộ phận truyền động để cải thiện môi trường làm việc và tăng tuổi thọ của thiết bị.
+ Quá nhiệt: Giám sát nhiệt độ và áp dụng các biện pháp làm mát hiệu quả để ngăn ngừa quá nhiệt trong quá trình hoạt động.
- Điều khiển:
+ Tiêu thụ năng lượng: Tối ưu hóa hệ thống điều khiển để giảm thiểu mức tiêu thụ năng lượng, đồng thời duy trì hiệu suất hoạt động cao.
+ Khởi động hệ thống: Đảm bảo quá trình khởi động diễn ra mượt mà và hiệu quả, tránh các sự cố có thể gây hư hỏng hoặc giảm hiệu suất của hệ thống.
Việc phân tích và tối ưu hóa các yếu tố trên giúp nâng cao hiệu suất tổng thể của hệ thống cơ điện tử, đảm bảo hoạt động ổn định và bền vững trong suốt quá trình sử dụng.
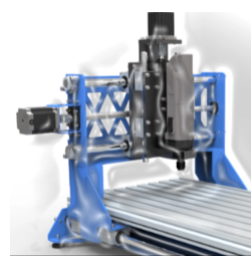
Hình 2. Máy phay CNC đã được tối ưu hóa kết cấu khung
- Giải quyết vấn đề của hệ thống cơ điện tử
+ Nguyên nhân gốc rễ không xác định cho các hiệu ứng suy thoái và sự cố: Việc thiếu thông tin chi tiết về các nguyên nhân gây ra sự suy giảm và hư hỏng trong hệ thống dẫn đến khó khăn trong việc phát hiện và khắc phục.
+ Mối quan hệ phụ thuộc không rõ ràng giữa các thành phần và tác động của chúng lên hành vi tổng thể: Việc không hiểu rõ mối quan hệ giữa các thành phần trong hệ thống và tác động của chúng đến hoạt động chung gây khó khăn trong việc tối ưu hóa và bảo trì.
+ Nguyên nhân không rõ ràng cho các vấn đề về độ chính xác: Các vấn đề liên quan đến độ chính xác thường không được xác định rõ ràng, dẫn đến hiệu suất kém và khó khăn trong việc cải tiến.
+ Giao tiếp khó khăn giữa các bộ phận phát triển khác nhau: Sự phối hợp giữa các phòng ban như thiết kế kết cấu, điều khiển và kỹ thuật phần mềm, và kiểm thử thường gặp trở ngại, gây ra sự chậm trễ và thiếu hiệu quả trong quá trình phát triển hệ thống.
Việc giải quyết các vấn đề trên đòi hỏi sự nghiên cứu kỹ lưỡng và hợp tác chặt chẽ giữa các bộ phận liên quan để cải thiện hiểu biết và tối ưu hóa hệ thống cơ điện tử.
- Đảm bảo hiểu biết toàn diện về hệ thống
+ Đảm bảo độ chính xác trong khi tăng cường hiệu suất: Nâng cao độ chính xác của hệ thống đồng thời cải thiện hiệu suất làm việc, tạo ra sản phẩm chất lượng cao hơn.
+ Cơ sở cho kỹ thuật hợp tác giữa các phòng ban: Tạo nền tảng vững chắc cho sự hợp tác giữa các bộ phận như thiết kế, điều khiển và kiểm thử, giúp tối ưu hóa quá trình phát triển sản phẩm.
- Các cơ chế cần xem xét
+ Cơ chế: Điều gì xảy ra bên trong hệ thống? Hiểu rõ các quá trình và hoạt động bên trong để có thể quản lý và điều khiển tốt hơn.
+ Độ nhạy: Yếu tố nào có ảnh hưởng đến kết quả? Xác định các yếu tố nhạy cảm và đánh giá tác động của chúng lên hệ thống.
+ Tiềm năng tối ưu hóa: Làm thế nào để cải tiến? Tìm kiếm các cơ hội cải tiến và áp dụng các biện pháp tối ưu hóa để nâng cao hiệu suất và hiệu quả của hệ thống.
c. Chiến lược, giải pháp
- Mô phỏng hệ thống toàn diện
Mô hình hóa hiệu quả hành vi của hệ thống thực tế với các yếu tố linh hoạt, tiếp xúc, khoảng cách, ma sát, tính phi tuyến trong truyền động (bao gồm cả hiệu ứng bão hòa của động cơ), và điện tử công suất.
- Các bước thực hiện:
+ Tích hợp chiến lược điều khiển: Kết hợp các phương pháp và quy trình điều khiển vào hệ thống để đảm bảo hoạt động hiệu quả.
+ Tham số hóa cài đặt bộ điều khiển: Điều chỉnh các thông số của bộ điều khiển để phù hợp với các yêu cầu cụ thể của hệ thống.
+ Xác định cài đặt bộ điều khiển bằng thuật toán tối ưu hóa: Sử dụng các thuật toán tối ưu hóa để tìm ra các cài đặt bộ điều khiển hiệu quả nhất, đảm bảo hệ thống hoạt động tối ưu và ổn định.
Việc áp dụng các chiến lược này sẽ giúp cải thiện đáng kể hiệu suất và độ chính xác của hệ thống, đảm bảo hoạt động ổn định và hiệu quả trong mọi điều kiện.
- Kiến trúc điều khiển theo tầng cho động cơ
+ Đầu vào của bộ điều khiển:
Tín hiệu phản hồi từ các cảm biến (vị trí, tốc độ, dòng điện)
Các giá trị tham chiếu (mục tiêu) cho vị trí, tốc độ, và dòng điện
Thông số môi trường và điều kiện vận hành thực tế
+ Đầu ra của bộ điều khiển:
Tín hiệu điều khiển đến các bộ phận truyền động (điện áp, dòng điện)
Tín hiệu điều chỉnh cho các bộ điều khiển cấp dưới
Thông tin phản hồi cho hệ thống giám sát và điều khiển cấp cao
Kiến trúc điều khiển theo tầng giúp đảm bảo sự phối hợp nhịp nhàng giữa các mức điều khiển khác nhau, từ điều khiển vi mô các thông số vận hành của động cơ đến điều khiển vĩ mô của toàn bộ hệ thống. Điều này giúp tối ưu hóa hiệu suất và độ ổn định của động cơ trong quá trình vận hành.
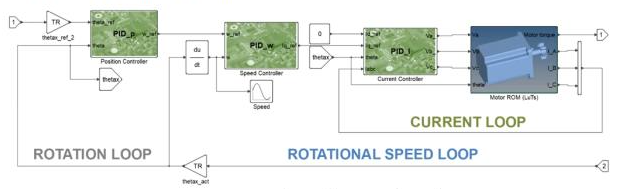
Hình 3. Các bộ điều khiển PID điều khiển động cơ
- Mô hình đại diện của động cơ
+ Yêu cầu: Cân bằng hợp lý giữa độ chính xác và thời gian tính toán
+ Các thành phần chính của mô hình:
Mạch điện:
Điện áp pha (Phase Voltage): Các đầu vào điện áp pha A, B, và C được sử dụng để mô phỏng điện áp đầu vào của động cơ.
Dòng điện pha (Phase Current): Các dòng điện pha A, B, và C được tính toán dựa trên điện áp đầu vào và các thông số của mạch điện.
Mạch điện (Electrical Circuit): Bao gồm các phần tử như cuộn cảm và điện trở của các pha A, B, và C.
- Biến đổi Park-Clarke (Park-Clarke Transformation):
Chuyển đổi D-Q: Sử dụng biến đổi Park-Clarke để chuyển đổi các tín hiệu pha thành các tín hiệu trục D và Q (Id và Iq).
Độ bão hòa (Saturation): Các tín hiệu Id và Iq được kiểm tra độ bão hòa để đảm bảo rằng các giá trị không vượt quá giới hạn định mức.
- Mô phỏng từ thông và mô-men xoắn:
Từ thông pha (Phase Flux): Mỗi pha A, B, và C có một hàm truyền (Transfer Function) để tính toán từ thông tương ứng.
Mô-men xoắn (Torque): Mô-men xoắn được tính toán dựa trên dòng điện và
từ thông.
- Các hàm truyền (Transfer Functions):
Các hàm truyền cho từ thông (Flux Transfer Functions): Các hàm này mô phỏng động lực học của từ thông trong mỗi pha.
Hàm truyền mô-men xoắn (Torque Transfer Function): Mô phỏng động lực học của mô-men xoắn tạo ra bởi động cơ.
- Các thành phần điều khiển:
Góc quay của rotor (Rotor Angle): Tín hiệu góc quay của rotor được tính toán và sử dụng trong các phép biến đổi.
Các phép tính toán toán học: Bao gồm các phép tính như chuyển đổi đơn vị, điều chỉnh góc, và các phép biến đổi khác để đảm bảo tín hiệu điều khiển chính xác.
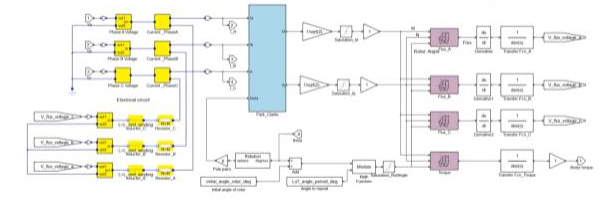
Hình 4. Sơ đồ khối điều khiển động cơ
Mô hình đại diện của động cơ kết hợp nhiều thành phần và phép biến đổi để mô phỏng chính xác các đặc tính điện từ và cơ học của động cơ. Mục tiêu là đạt được sự cân bằng hợp lý giữa độ chính xác của mô phỏng và thời gian tính toán, đảm bảo hệ thống có thể hoạt động hiệu quả và đáng tin cậy trong các điều kiện vận hành thực tế.